30 years old but FOREVER JUNG
The UNITED GRINDING Group has not only provided its customers with new systems and made them more successful for three decades, but it also provides them with vital services such as rebuilds, which make outdated machines as good as new
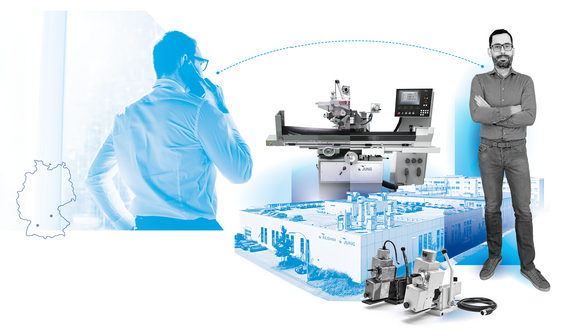
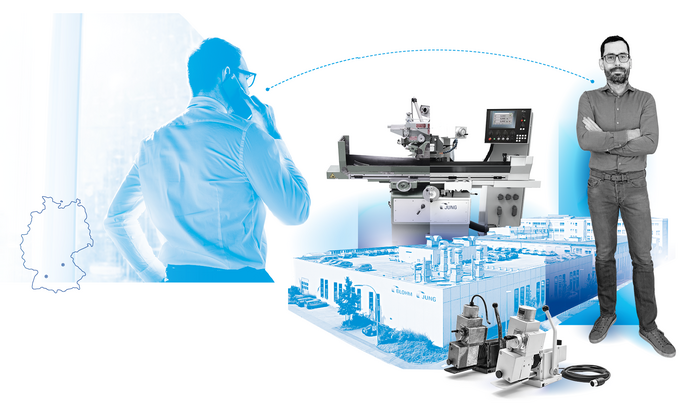
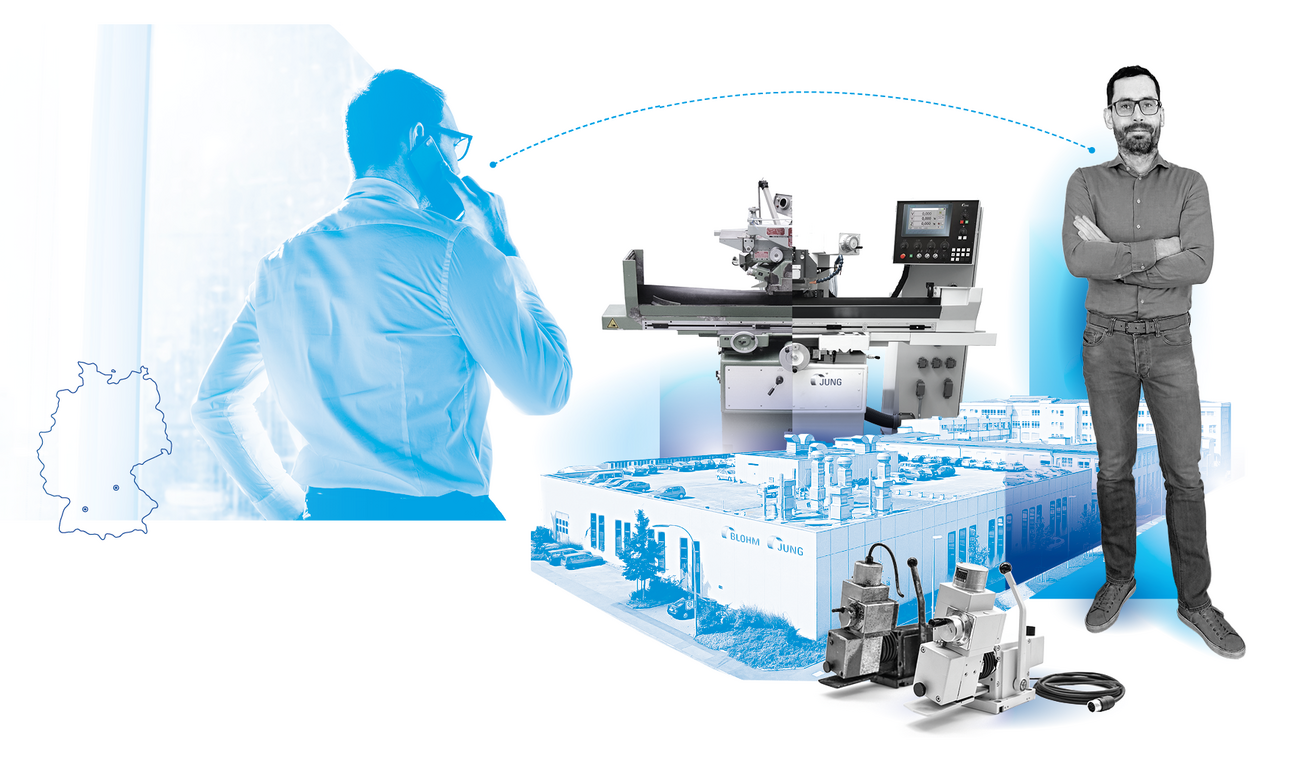
It’s a sunny afternoon in Fürth, the sound of birds chirping in the city park mingles with noises from JUNG grinding machines coming from the windows of an old building in the city center.
“Mr. Dorn, where can I reach you, do you have time to talk?”
“Mr. Friedrich, how nice it is to hear from you! Wait, I’ll go to the office for a moment, we can talk better there.”
“Wonderful. I just wanted to hear whether everything was OK with your five JUNG machines. Your next preventive maintenance appointment is coming up.”
“Of course, everything is fine, as always. Or, as we say here: Forever JUNG!”
Reiner Dorn is Managing Director of Reichenbächer + Hasel Schleiftechnik GmbH, a successful company specializing in the highest precision for surface and profile grinding technology. Their customers include well-known companies from the electronics, medical technology, machine tool, mold and tool making, aerospace, and automotive industries. Since its foundation in 1971, the company has relied exclusively on JUNG machines.
“That’s good to hear, Mr. Dorn. Of course, our technician will still come by to check everything in detail.”
Matthias Friedrich, Sales Engineer at BLOHM JUNG, provides top technical support for revision requests from customers. Due to the high quality and longevity of JUNG machines, there are still around 15,000 models in use worldwide that are no longer manufactured. This also applies to the JE 525 machines at Reichenbächer + Hasel, which were built between 1989 and 1990. For these customers, OEM maintenance, inspection, and machine rebuilds are highly valued services.
“Is everything OK with the two latest rebuilds?”
“Mr. Friedrich, these machines are still as good as new. We just had the rebuilds done a few years ago. In any case, our customers can continue to rely on the usual high standards of precision. It also greatly reduces our energy consumption, which many of our customers insist on for their products.”
“Yes, you’re right, of course. JUNG machines have a top-grade cast steel base. The rebuild process means that the energy used to produce the machine the first time round is also used for a second machine life, which has a much lower energy footprint compared to building a new machine.”
A complete overhaul (rebuild) of a machine at the JUNG plant in Göppingen breathes new life into old equipment. It is then as good as it was when first delivered and is just as easy to operate. After a rebuild, the service life of the machine is reset to up to several decades and the customer receives a machine that is as good as new at an economical price.
How a rebuild is done
A machine overhaul can either be for the complete machine or for individual modular components. If the entire machine is refurbished, we call this a rebuild. Although the process can take several weeks at the Göppingen plant, customers can continue production without losing much time at all. This is because they either receive a comparable as-new overhauled machine directly in exchange for their old machine, or they are provided with a loaner machine for the duration of the overhaul.
Guideways
The guideways are crucial for the precision and longevity of JUNG machines. As an exclusive JUNG service for customers, these are ground in during the rebuild process. They are given a special surface hardening treatment and the proven cross-hatch finish, which ensures the necessary accuracy for medical technology and the automotive industry, among others.
Grinding spindles
One of the most stressed and important components is the grinding spindle, which is in direct contact with the workpiece and determines its quality. Grinding spindles are replaced when a machine is overhauled.
Repainting
Fashions change, even for grinding machines: in the past, green was the color of choice, but today gleaming white is much more modern. After a rebuild, your JUNG machine will look like a newly built machine.
Dressing
The dressing unit in the machine sharpens and shapes the grinding wheel. The rebuild team in Göppingen restores it to an as-new condition for maximum precision by replacing spare and wear parts and grinding the guides.
Upgrades
Outdated grinding equipment can also benefit from technical progress without having to replace the entire machine. An updated machine control, a new automatic centralized lubrication system, or new capabilities, such as creep feed, plunge grinding, or face grinding, are just a few examples.
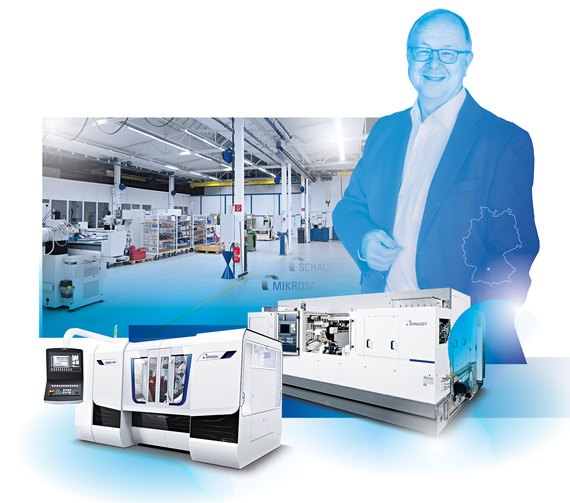
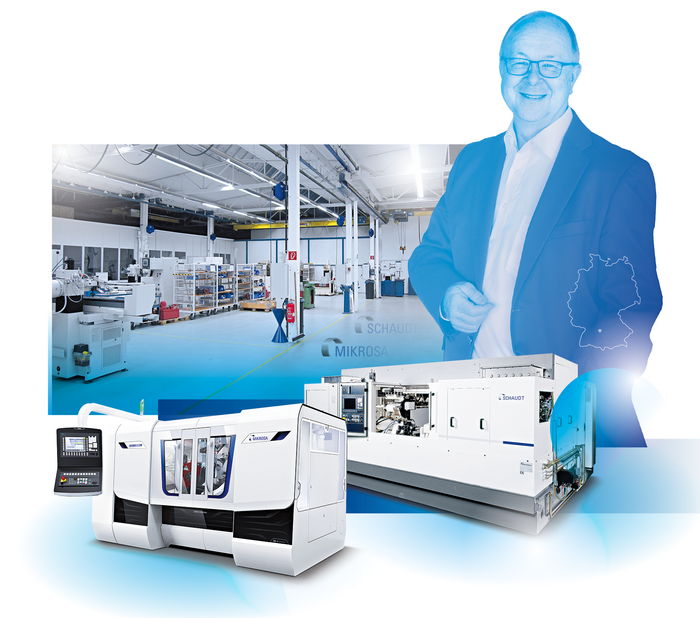
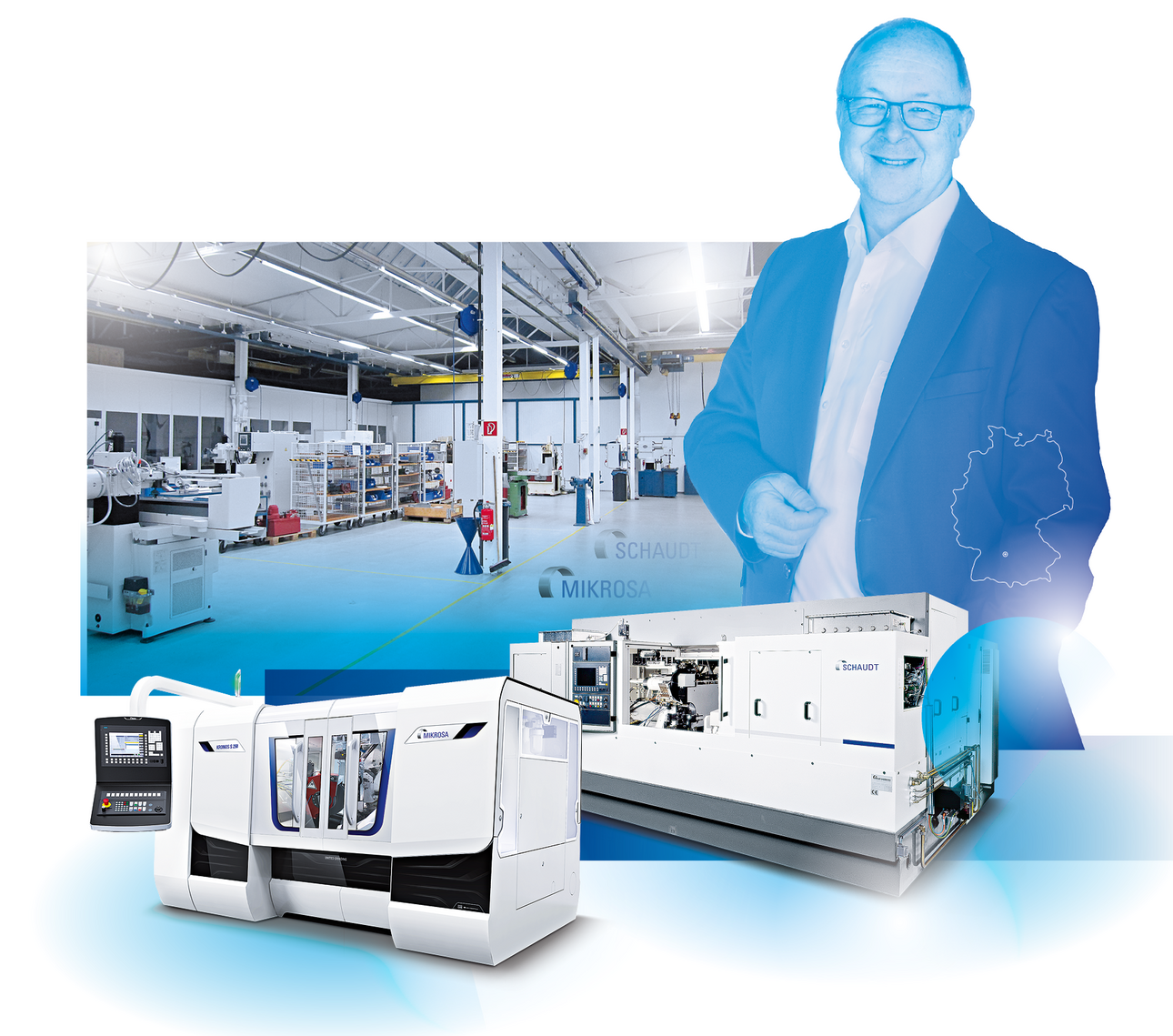
SCHAUDT AND MIKROSA AS GOOD AS NEW TOO
Thanks to UNITED GRINDING’s maintenance and rebuild service, thousands of SCHAUDT and MIKROSA machines are still in use today. “The life expectancy of grinding machines is longer than that of other machine tools. Because we have taken over the support of these models, there is no reason for our customers to replace them, even if no new ones are being built,” says Ralf Schürl, Head of Technology at the Göppingen site of BLOHM JUNG. The technology center in Göppingen is currently being modernized and expanded to make it even more efficient. “Because, where a relatively small JUNG machine requires only around six square meters (64.5 square feet) of installation space, a SCHAUDT can take up to 40 square meters (430 square feet).”
The highly productive CamGrind L2 as a cylindrical and non-cylindrical grinding machine for producing medium and large series was specially designed to manufacture camshafts for combustion engines. However, it is extremely versatile and can be configured for other workpieces within a few days. Conversions of this kind are also performed in Göppingen, says Schürl. For example, by exchanging wheel guards on machines that use the multi-wheel concept developed by SCHAUDT, which allows all the cylindrical features of a workpiece to be ground in a single plunge. Another important service provided by the Göppingen site is the overhaul of individual components for machines in the field, which are then installed by experts at the customer’s site. In addition to the CamGrind, our customers also use numerous FlexGrind machines and we provide the same service for these units as well. This versatile cylindrical grinding machine from SCHAUDT has clamping lengths of up to 4,000 millimeters (157 inches) and component weights of up to 1,200 kilograms (2,640 lbs). It is used for grinding tool spindles, printing rolls, and workpieces with individual forms.
More than 100 years of grinding history—and still in demand
The Göppingen team consists of specialists in mechanical and electrical design, software, and process development. They are supported by employees from the Service department. In addition to the SCHAUDT systems, they also take care of MIKROSA machines.
The origins of this long-established company go back to 1878. Their state-of-the-art Kronos S, M, L, and D series are renowned for their highly productive centerless grinding of precision workpieces. “The Kronos S-series, with its cross slide system design for very high accuracy, is still unique on the market,” says Schürl. And thanks to the outstanding rebuild and maintenance service with the know-how of the original manufacturing company, customers can use their SCHAUDT and MIKROSA machines for successful production for many more years to come.
Ralf Schürl on the rebuild variants:
Our Rebuild concepts are tailored to the customers' needs. For example, Rebuild @ the customer: This is where the machine is overhauled at the customer’s plant. This is possible up to a certain extent. Only more complex tasks, such as the rebuilding and upgrading of the guideway system are done at our site in Göppingen. We give our customers logistical support.
The second concept is called Second Life. A machine is bought back from the market from a third party and overhauled at our premises in Göppingen. This machine is then available on the market again. Customers can increase their capacity for established processes or develop workflows for new workpieces with the support of our experts.